Fixing a steel structure warehouse involves a systematic approach to identify, assess, and address various issues related to structural integrity, maintenance, repairs, and upgrades. Steel structure warehouses are common in industrial and commercial settings, providing durable and versatile storage solutions. Over time, these warehouses may experience wear and tear, structural problems, corrosion, or other issues that require attention to ensure their functionality, safety, and longevity. Here’s a comprehensive guide on how to fix a steel structure warehouse:
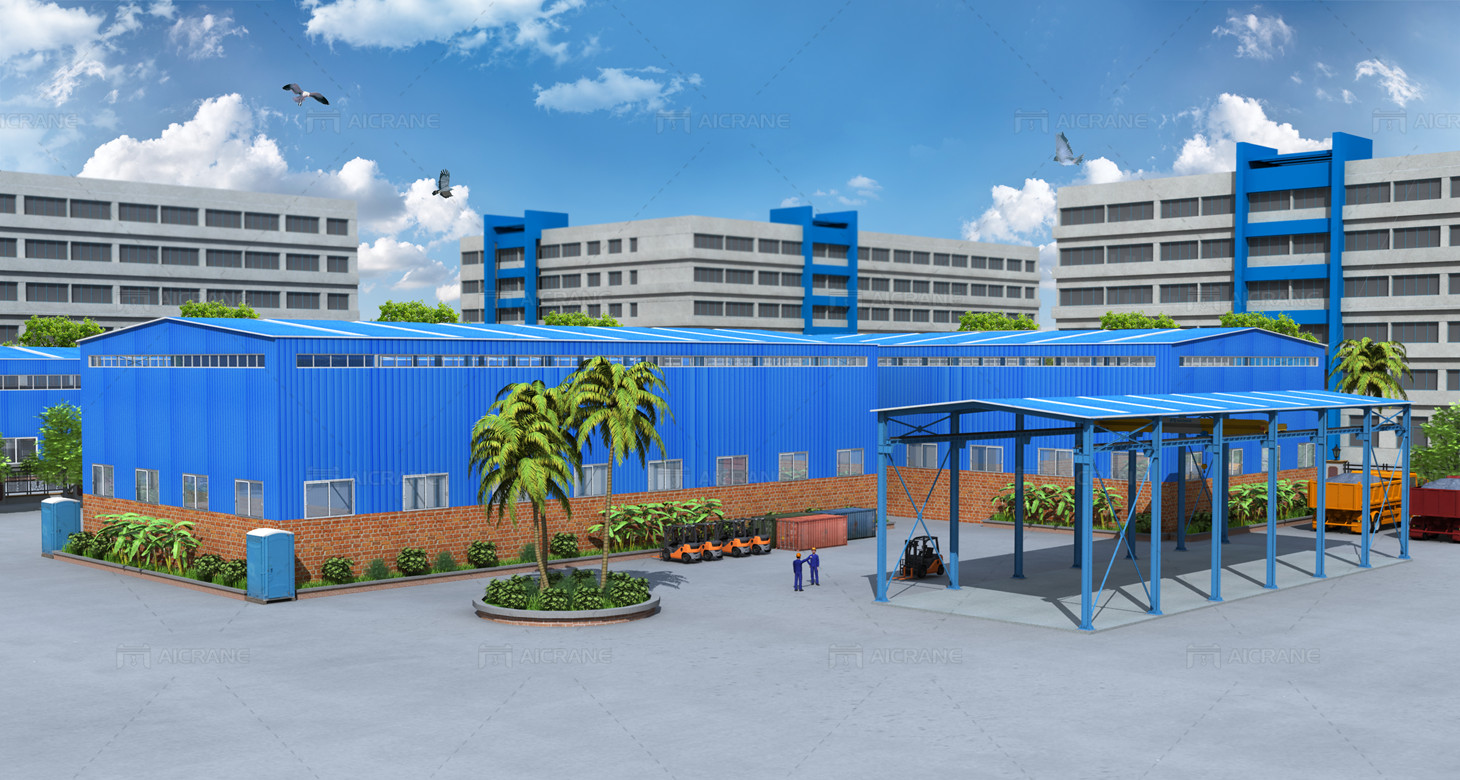
Structural Inspection and Assessment
Start by conducting a thorough inspection and assessment of the steel structure warehouse. This includes examining the foundation, columns, beams, trusses, roof, walls, doors, windows, flooring, and other structural elements. Look for signs of damage, corrosion, rust, deformation, cracks, leaks, or deterioration. Use structural engineering tools, equipment, and techniques to assess the overall condition and structural integrity of the warehouse.
Identify Problem Areas and Prioritize Issues
Based on the inspection findings, identify problem areas and prioritize issues that require immediate attention. Determine whether the structural problems are minor, such as surface corrosion or cosmetic damage, or major, such as structural instability or safety hazards. Categorize issues into critical, urgent, and routine maintenance tasks to develop an action plan for fixing the warehouse.
Repair and Reinforcement of Structural Elements
Address structural issues by implementing repair and reinforcement measures for the steel elements. This may involve welding repairs for damaged beams, columns, or joints, replacing corroded or weakened sections, adding steel braces or plates for reinforcement, or strengthening connections and supports. Use certified welding procedures, quality materials, and skilled welders to ensure structural integrity and compliance with safety standards.
Corrosion Protection and Coating
Protect steel surfaces from corrosion and rust by applying protective coatings and treatments. Clean and prepare steel surfaces by removing rust, dirt, grease, and contaminants before applying coatings. Use corrosion-resistant paints, primers, sealants, or galvanizing techniques to create a barrier against moisture, chemicals, and environmental factors. Regularly inspect and maintain coatings to prevent corrosion and maintain aesthetics.
Roof and Wall Repairs
Inspect and repair the roof and walls of the warehouse to prevent leaks, water damage, and structural issues. Seal gaps, joints, and seams in the roof and wall panels to prevent water infiltration. Replace damaged or deteriorated roofing materials, flashing, gutters, downspouts, and insulation as needed. Ensure proper drainage, ventilation, and insulation to protect the interior from moisture, heat, and cold.
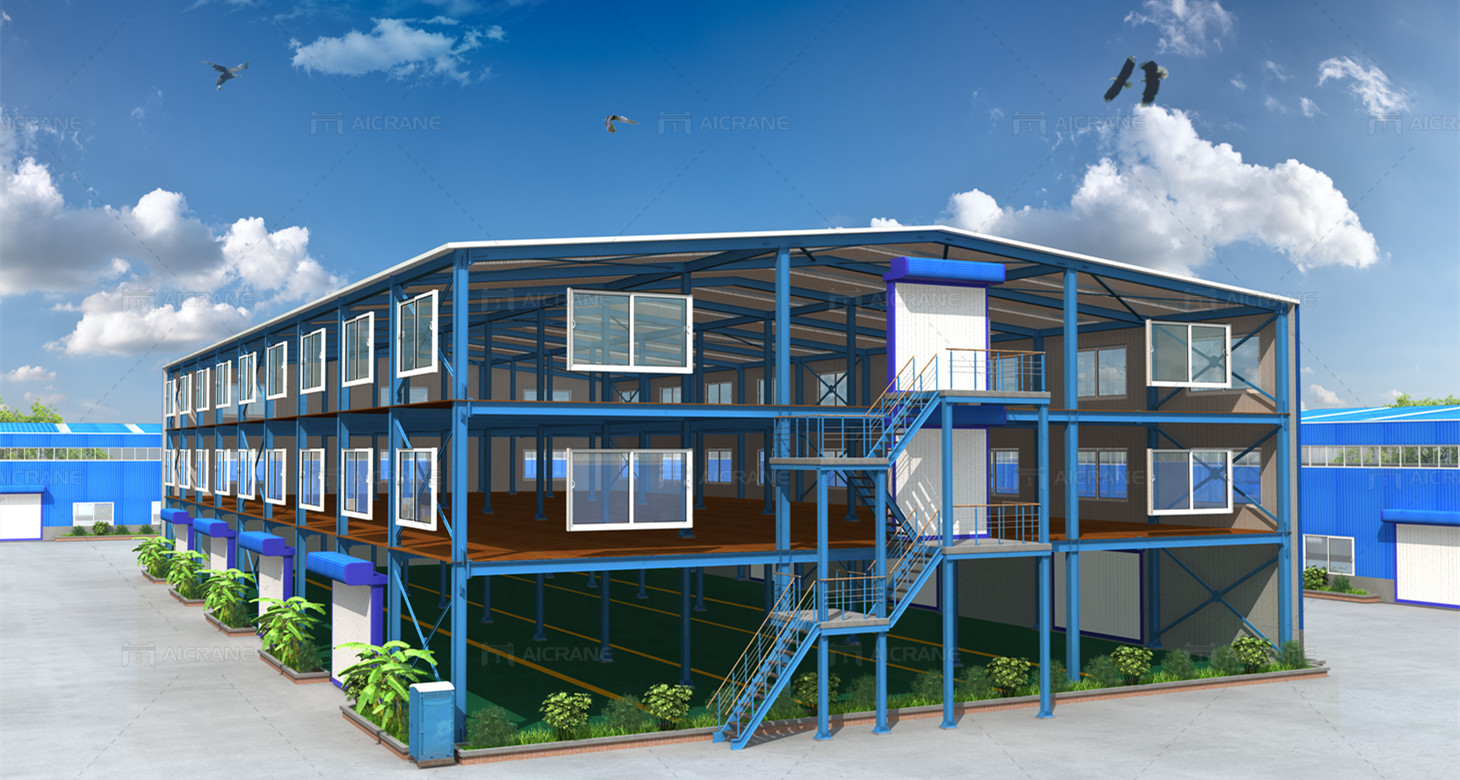
Door and Window Maintenance
Check and maintain doors, windows, and openings in the warehouse for smooth operation, security, and weatherproofing. Lubricate hinges, tracks, rollers, and locking mechanisms of doors and windows. Repair or replace damaged seals, weather stripping, handles, and locks to improve energy efficiency and security. Consider upgrading to insulated doors or windows for better thermal performance.
Flooring Repairs and Upgrades
Evaluate the condition of the warehouse flooring and perform repairs or upgrades as necessary. Repair cracks, spalling, or uneven surfaces in concrete floors to prevent trip hazards and damage to equipment. Apply epoxy coatings, sealants, or floor treatments for improved durability, chemical resistance, and aesthetics. Consider installing anti-slip coatings or markings for safety in high-traffic areas.
Electrical and Lighting Upgrades
Inspect and upgrade electrical systems, lighting fixtures, and safety devices in the warehouse. Ensure that electrical wiring, outlets, switches, and circuit breakers are in good condition and comply with electrical codes. Upgrade to energy-efficient LED lighting for better illumination, cost savings, and environmental benefits. Install emergency lighting, exit signs, fire alarms, and smoke detectors for safety compliance.
HVAC System Maintenance
Maintain and service heating, ventilation, and air conditioning (HVAC) systems in the warehouse for optimal comfort, air quality, and energy efficiency. Clean or replace air filters, ductwork, vents, and fans regularly to prevent dust buildup and airflow restrictions. Inspect and repair HVAC equipment, controls, thermostats, and refrigerant levels for proper functioning and energy savings.
Fire Protection and Safety Measures
Ensure that the warehouse has adequate fire protection and safety measures in place. Install fire extinguishers, smoke detectors, sprinkler systems, fire alarms, emergency exits, and signage according to building codes and regulations. Conduct fire drills, safety training, and emergency response procedures for warehouse personnel. Inspect fireproofing materials, barriers, and containment systems for fire safety.
Professional Consultation and Compliance
Consult with structural engineers, architects, contractors, and safety experts for professional advice and guidance on fixing the steel structure warehouse. Obtain necessary permits, approvals, and compliance certificates for structural repairs, renovations, or upgrades. Follow industry standards, building codes, safety regulations, and environmental guidelines throughout the fixing process.
Regular Maintenance and Monitoring
Implement a regular maintenance program and monitoring schedule for the steel structure construction warehouse to prevent future problems and ensure ongoing functionality. Conduct routine inspections, maintenance checks, and condition assessments of structural elements, equipment, systems, and facilities. Keep maintenance records, logs, and documentation for compliance, warranty support, and historical reference.
By following these steps and best practices, you can effectively fix a steel structure warehouse, address structural issues, enhance durability, safety, and functionality, and prolong the lifespan of the facility. Regular maintenance, proactive repairs, and professional consultation are key to maintaining a well-maintained and reliable warehouse environment. Contact a reliable steel structure manufacturer to learn more about this.