Rail mounted gantry cranes (RMG cranes) are vital components in industries that require heavy lifting and precise handling of large loads, such as container terminals, shipyards, and large-scale manufacturing plants. These cranes operate on fixed rails, which must be installed and maintained with precision to ensure the safe and efficient functioning of the crane. Fixing the rails for these massive rail mounted gantry cranes involves a series of meticulous steps, each of which is critical for the overall performance and safety of the system.
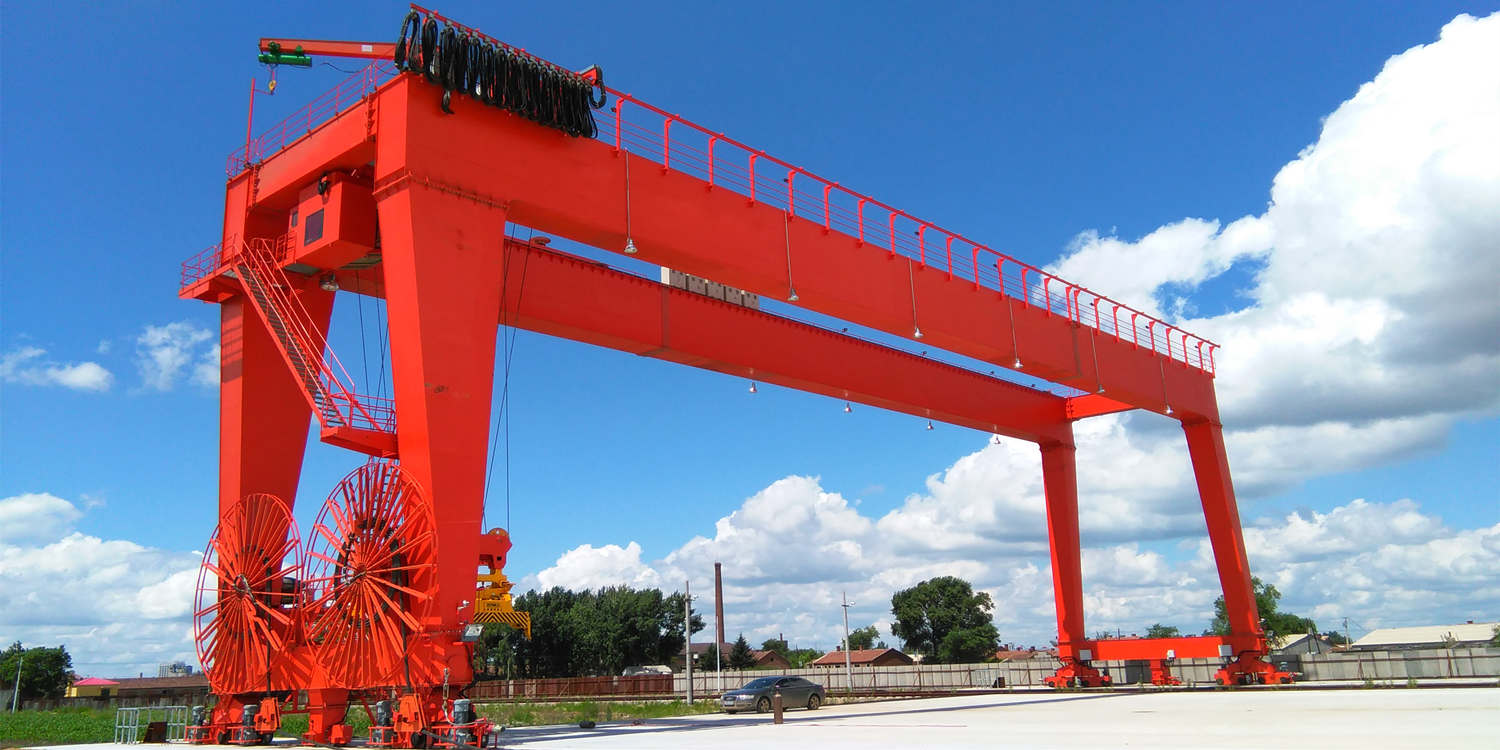
Understanding the Importance of Proper Rail Installation
Before diving into the specifics of how to fix rails for rail mounted gantry cranes, it’s important to understand why this process is so crucial. The rails provide the path along which the gantry crane moves, and any misalignment or instability in the rails can lead to significant operational issues. These may include increased wear and tear on the crane’s wheels, misalignment of the crane’s structure, reduced efficiency, and even catastrophic failures. Therefore, fixing the rails correctly is not just a matter of installation; it’s about ensuring long-term operational safety and performance.
Steps to Fix Rails for Rail Mounted Gantry Cranes
1. Site Preparation and Surveying
The first step in fixing rails for RMG cranes is thorough site preparation. This involves clearing the area of any debris and ensuring that the ground is stable and capable of supporting the weight of both the mobile gantry crane and the loads it will carry. A comprehensive geotechnical survey should be conducted to assess the soil condition and to determine whether any special foundation work is required.
Precise surveying is also essential at this stage. The alignment of the rails must be exact, so detailed measurements are taken to establish the rail path, including the distance between rails (gauge), elevation, and alignment. Any deviation from the design specifications at this stage can lead to misalignment, which can cause operational inefficiencies or even accidents.
2. Foundation Work
The foundation is the backbone of the rail system. Depending on the soil conditions and the load requirements, the foundation may need to be reinforced with concrete or other materials to ensure it can support the rails and the crane’s weight. The foundation must be level and strong enough to prevent any movement or settling over time, which could cause misalignment of the rails.
For RMG heavy duty cranes, deep foundations such as piles might be necessary. In such cases, the piles are driven into the ground to reach stable soil layers, and a concrete foundation is then poured over them. The foundation should also include drainage systems to prevent water accumulation, which can weaken the structure over time.
3. Laying the Rail Bed
Once the foundation is prepared, the next step is laying the rail bed. The rail bed consists of a layer of crushed stone or gravel that provides a stable and level surface for the rails. The bed also acts as a drainage layer, helping to prevent water accumulation around the rails. This layer should be compacted to ensure it is firm and stable, and it should be level across its entire length to ensure consistent rail alignment.
A high-quality rail bed is essential for minimizing vibrations and shocks during crane operations, which can otherwise lead to accelerated wear of both the rails and the crane’s wheels.
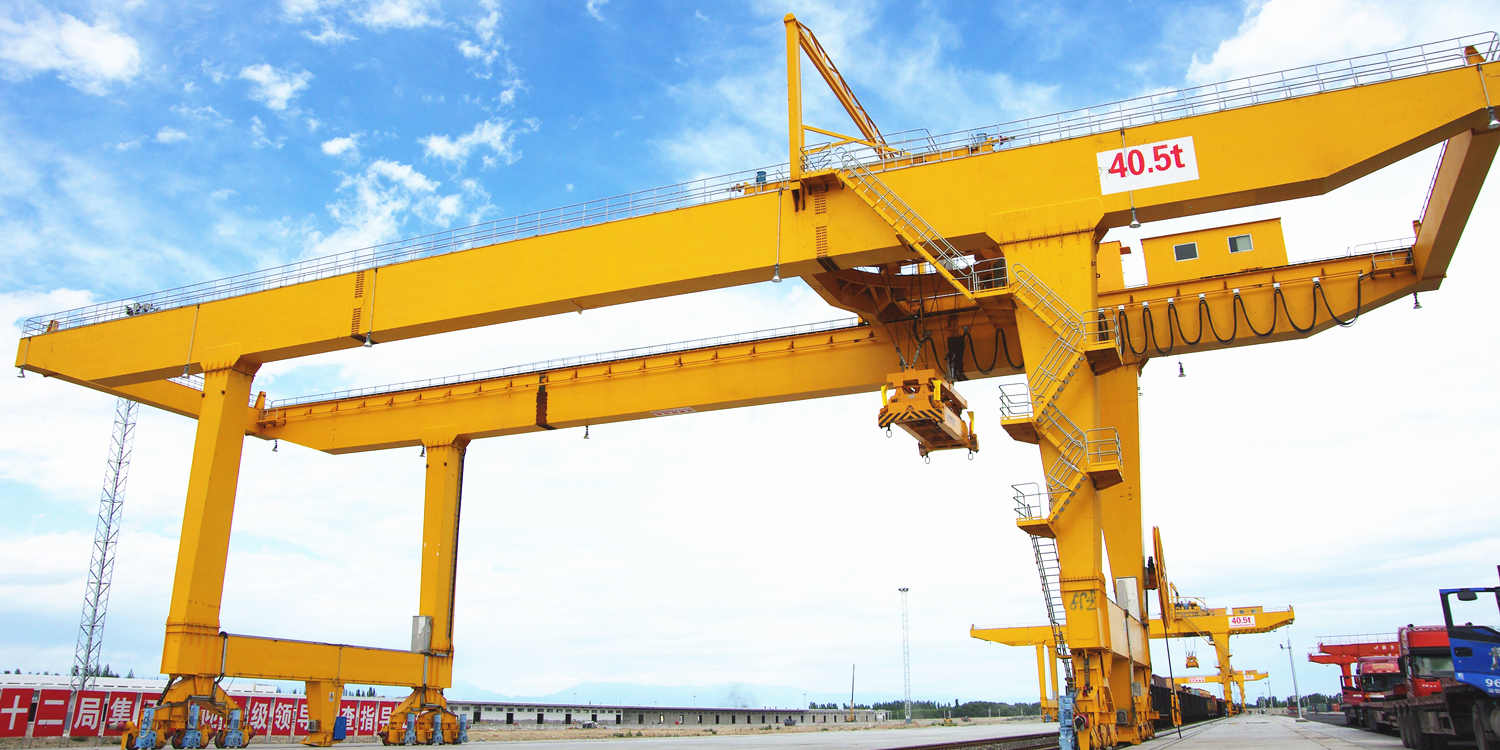
4. Placing and Aligning the Rails
The actual placement of the rails is a critical step in the process. Rails for RMG cranes are typically made of high-strength steel and come in pre-fabricated lengths. These rails need to be laid on the rail bed and aligned precisely according to the design specifications.
The rails are typically positioned using specialized rail alignment tools that ensure the correct gauge (distance between the rails), straightness, and levelness. The rails should be placed so that their joints are staggered, which helps to distribute the load more evenly and reduces the risk of weak points developing along the rail path.
Rail Clips and Fasteners:
Once the rails are in place and properly aligned, they need to be secured using rail clips or fasteners. These components are designed to hold the rails firmly in place, preventing any lateral or vertical movement during crane operations. The choice of clips or fasteners depends on the design of the crane and the rail system, but they are typically made of durable materials like steel to withstand the forces exerted by the crane.
Rail clips are bolted into the concrete foundation or base plates, and they must be installed with the correct torque to ensure they hold the rails securely without causing any deformation. In some cases, elastomeric pads may be placed between the rails and the foundation to absorb vibrations and reduce noise.
5. Joint Welding and Finishing
After the rails are placed and secured, the joints between rail sections need to be welded or bolted together. In heavy-duty applications, welding is often preferred because it creates a continuous rail surface, reducing wear on the crane’s wheels and minimizing the risk of misalignment over time.
Welding:
When welding the rail joints, precision is crucial. The welds must be smooth and even, with no irregularities that could interfere with the crane’s movement. After welding, the joints are typically ground smooth to ensure a seamless transition between rail sections.
Bolted Joints:
In some cases, bolted joints are used instead of welding. Bolted joints can be advantageous in situations where future rail adjustments or replacements may be necessary. However, they must be installed with precision to avoid any gaps or misalignment.
6. Rail Alignment Verification
Once the rails are installed, a final alignment check is essential. This involves using precise measuring instruments to verify that the rails are straight, level, and correctly spaced. Any deviations from the design specifications should be corrected before the crane is put into operation.
The alignment check should also include a test run of the crane along the rails. This allows operators to ensure that the crane moves smoothly without encountering any resistance or vibration that could indicate misalignment or other issues.
7. Maintenance and Inspection
After the installation is complete, regular maintenance and inspection of the rails are necessary to ensure their continued performance. This includes checking the rail alignment, inspecting the rail clips and fasteners for wear or loosening, and monitoring the condition of the rail joints. Any issues detected during these inspections should be addressed promptly to prevent more serious problems from developing. Some crane manufacturer like Aicrane provides this kind of service.
Fixing rails for rail mounted gantry cranes is a complex process that requires careful planning, precise execution, and ongoing maintenance. Proper rail installation is critical to the safe and efficient operation of RMG cranes, and it involves a series of meticulous steps, from site preparation and foundation work to rail alignment and final verification. By following these steps and adhering to best practices, operators can ensure that their rail mounted gantry cranes function reliably and efficiently, minimizing downtime and maximizing productivity in their operations.