Straddle carriers are essential pieces of equipment in ports and container terminals, playing a crucial role in handling and transporting containers efficiently. The weight of a straddle carrier, often referred to as straddle carrier weight, significantly impacts its performance, operational efficiency, and maintenance requirements. Several factors influence straddle carrier weight, including design specifications, materials used, capacity, technological features, and operational conditions. Understanding these factors is vital for optimizing the performance and longevity of straddle carriers.
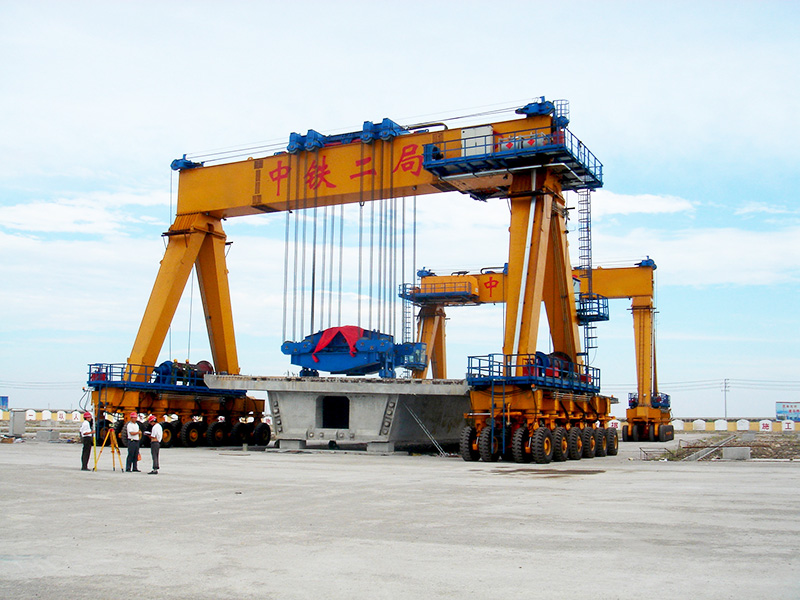
Design Specifications
Structural Design
The structural design of a straddle carrier is one of the primary factors determining its weight. Different designs, such as single-beam or double-beam structures, have varying weight implications. A double-beam structure generally provides greater stability and strength, but it also increases the overall weight of the carrier.
Dimensions
The overall dimensions of the straddle carrier, including height, width, and length, play a crucial role in its weight. Larger dimensions typically mean more material is used in construction, thus increasing the weight. However, larger carriers can handle larger loads and provide greater operational flexibility.
Wheel Configuration
The number and type of wheels or tires used in a straddle carrier affect its weight. A configuration with more wheels, such as an eight-wheel setup, provides better load distribution and stability but also adds to the overall weight compared to a four-wheel configuration.
Materials Used
Steel Components
The type of steel used in the construction of the straddle carrier’s frame and other components significantly influences its weight. High-strength, low-alloy steels are often used to achieve a balance between strength and weight. While stronger steel can reduce the thickness of components and thus the overall weight, it might also increase the cost.
Composite Materials
The use of composite materials, such as carbon fiber or reinforced plastics, can reduce the weight of straddle carriers. These materials offer high strength-to-weight ratios and are increasingly being used in modern straddle carrier designs. However, they can be more expensive than traditional materials.
Tires
The type of tires used, whether solid rubber or pneumatic, also impacts the weight. Pneumatic tires are generally lighter and provide better shock absorption, while solid rubber tires are heavier but more durable and puncture-resistant.
Load Capacity
Maximum Load
The maximum load capacity of a straddle carrier heavy duty gantry crane is directly related to its weight. Carriers designed to handle heavier loads require stronger and often heavier components to ensure safety and durability. Therefore, a straddle carrier with a higher load capacity will typically weigh more than one with a lower capacity.
Load Distribution
The design considerations for load distribution also affect weight. A straddle carrier must be designed to evenly distribute the weight of the load across its structure to prevent excessive wear and tear on any single component. This often involves using additional structural elements, which can increase the overall weight.
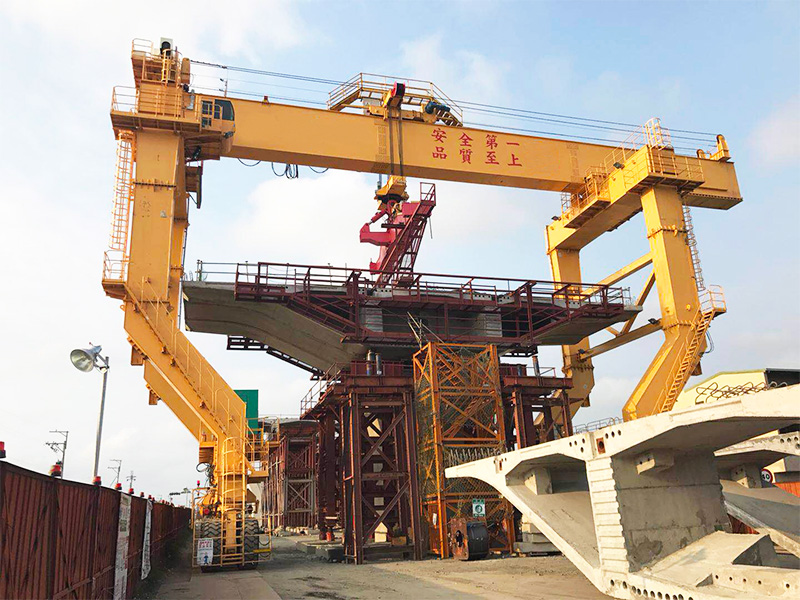
Technological Features
Automation Systems
Modern straddle carriers often include advanced automation systems for improved efficiency and safety. These systems, including sensors, cameras, and control units, add to the overall weight of the carrier. However, the benefits of improved operational efficiency and reduced labor costs often outweigh the additional weight.
Energy Systems
The type of energy system used, whether diesel, electric, or hybrid, also influences the weight. Electric and hybrid systems may include heavy battery packs or additional components for energy conversion, adding to the weight. However, these systems can offer environmental benefits and reduced operational costs.
Hydraulic Systems
The hydraulic systems used for lifting and steering also contribute to the straddle carrier weight. More advanced hydraulic systems with higher capacity and precision control typically weigh more due to the larger and more complex components involved.
Operational Conditions
Environmental Factors
The operating environment of the straddle carrier affects its design and weight. Carrier cranes used in harsh conditions, such as extreme temperatures or corrosive environments, require additional protective measures, such as thicker paint coatings or corrosion-resistant materials, increasing the weight.
Usage Frequency
The frequency and intensity of use also impact the design and weight of straddle carriers. Carriers that operate continuously or handle high volumes of cargo need to be more robust and durable, which often translates to additional weight in the form of reinforced structures and components.
Maintenance Requirements
Maintenance considerations also play a role in the overall weight. Straddle carriers designed for easier maintenance may include additional access points, ladders, or platforms, which add to the weight but improve operational efficiency by reducing downtime for repairs and servicing.
The weight of a straddle carrier, or straddle carrier weight, is influenced by a combination of design specifications, materials used, load capacity, technological features, and operational conditions. Each of these factors contributes to the overall performance, efficiency, and longevity of the straddle carrier. By understanding and optimizing these factors, manufacturers and operators can ensure that their straddle carriers meet the demands of modern container handling while maintaining high standards of safety and reliability. Balancing these elements is key to achieving the optimal straddle carrier weight for specific operational needs.