Rubber-tired gantry cranes (RTGs) are essential for efficient container handling in ports, intermodal terminals, and various industrial applications. These cranes are highly versatile and offer significant flexibility due to their mobility, allowing them to move between different locations within a site. Installing rubber-tired gantry cranes onsite involves several critical steps, each requiring careful planning, precise execution, and adherence to safety protocols. This passage outlines the comprehensive process for the successful installation of rubber-tired gantry cranes onsite.
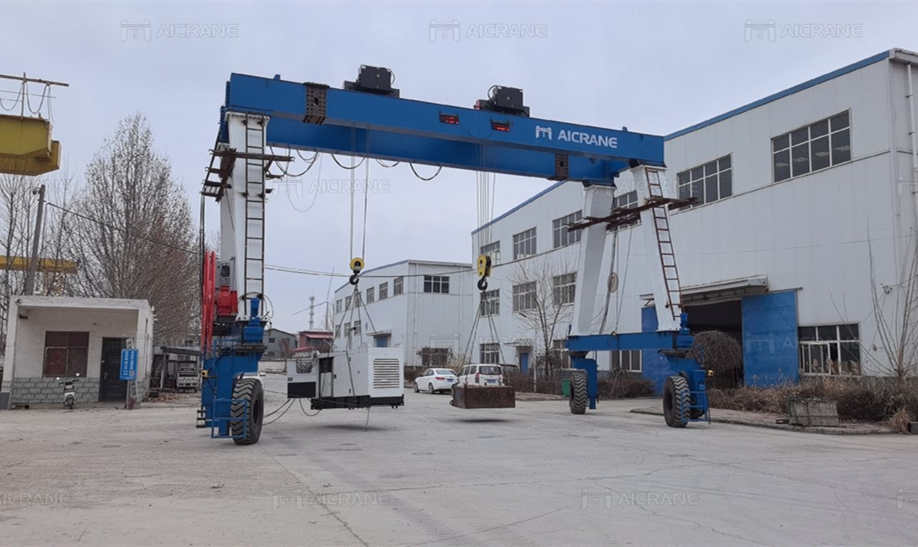
Site Preparation
The first step in installing rubber-tired gantry cranes is preparing the site. This involves conducting a thorough site survey to identify potential obstacles, uneven surfaces, and any existing infrastructure that might interfere with the installation. The survey should include:
Assessment of Ground Conditions: Ensuring that the ground can support the crane’s weight and operations without excessive settlement.
Clearance of Obstacles: Removing any physical obstacles, debris, and unnecessary equipment from the installation area.
Marking of Installation Area: Clearly marking the boundaries of the installation site to facilitate accurate placement and alignment of the crane.
Delivery and Unloading
Once the site is prepared, the next step is the delivery and unloading of the crane components. The components of rubber-tired gantry cranes are usually transported in sections to the installation site. This process involves:
Coordination with Transporters: Ensuring that the transportation of crane components is coordinated with the installation schedule to avoid delays.
Unloading Equipment: Using suitable unloading equipment such as mobile cranes or forklifts to safely unload the crane components.
Inspection of Components: Conducting a thorough inspection of the delivered components to ensure that there are no damages or missing parts.
Assembly of Crane Components
Assembling the crane components is a critical phase in the installation process. This step involves:
Following Manufacturer Guidelines: Adhering to the manufacturer’s assembly instructions and guidelines to ensure the crane is assembled correctly.
Positioning Major Components: Carefully positioning the major components such as the gantry structure, legs, and beams in their respective places.
Securing Connections: Using appropriate fastening techniques to secure connections between components. This includes bolting, welding, and other methods specified by the gantry crane manufacturer.
Use of Precision Tools: Employing precision tools and instruments to ensure that the components are aligned accurately and securely fastened.
Installation of Electrical and Hydraulic Systems
Rubber-tired gantry cranes are equipped with complex electrical and hydraulic systems that require careful installation. This includes:
Electrical Wiring: Installing the electrical wiring for power supply, control systems, and lighting. This must be done according to the electrical schematics provided by the manufacturer.
Hydraulic Systems: Setting up the hydraulic systems that operate the crane’s movement and lifting mechanisms. This involves connecting hydraulic hoses, installing pumps, and ensuring that the system is free of leaks.
Control Systems: Integrating control systems that allow operators to control the crane’s movements and operations. This includes setting up the operator’s cab, installing control panels, and configuring the software.
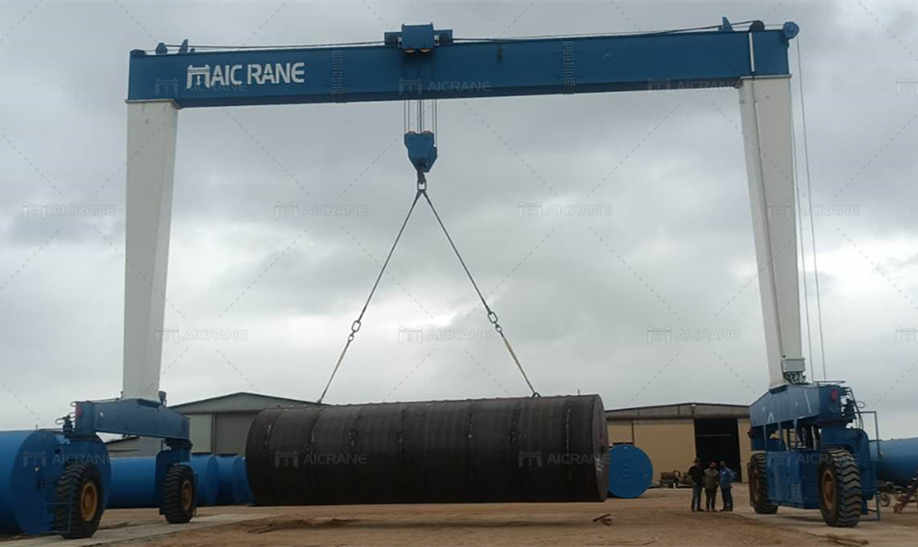
Testing and Calibration
Before the crane can be put into operation, it must undergo rigorous testing and cvalibration to ensure that all systems are functioning correctly and safely. This involves:
Load Testing: Conducting load tests to verify that the crane can handle the specified load capacities without any issues. This includes static and dynamic load testing.
Functionality Tests: Testing all the functions of mobile gantry crane, including movement, lifting, and safety systems, to ensure they operate as intended.
Calibration: Calibrating the control systems and sensors to ensure precise operation. This may involve adjusting the settings of the control software and aligning the sensors.
Safety Inspections
Safety is paramount when installing rubber-tired gantry cranes. Before the gantry crane is handed over for regular use, it must pass a series of safety inspections. This includes:
Compliance Checks: Ensuring that the installation complies with all relevant safety standards and regulations.
Safety Features: Verifying that all safety features such as emergency stop buttons, alarms, and limit switches are functioning correctly.
Operator Training: Providing comprehensive training for operators and maintenance personnel on the safe operation and maintenance of the crane.
Final Handover
The final step in the installation process is the handover of the crane to the client. This involves:
Documentation: Providing all necessary documentation, including installation records, test certificates, and operation manuals.
Demonstration: Conducting a demonstration of the crane’s functions and safety features to the client’s personnel.
Sign-off: Obtaining a sign-off from the client to confirm that the installation is complete and meets all specified requirements.
The installation of rubber-tired gantry cranes onsite is a complex process that requires meticulous planning, precise execution, and strict adherence to safety protocols. From site preparation to final handover, each step must be carefully managed to ensure the successful deployment of these versatile cranes. By following the outlined steps and paying close attention to detail, businesses can ensure that their rubber-tired gantry cranes are installed efficiently, safely, and ready for reliable operation.